Nissan Sunderland Case Study
The automobile sector remains one of the few major manufacturing industries in the UK. Over 1.5 million new vehicles are produced annually within the country, predominantly at seven major manufacturing facilities. These plants are owned by foreign-based transnational corporations (TNCs), including Nissan, Toyota, and BMW.
Car manufacturing was not sustainable in the past due to inefficient engines producing toxic pollutants, parts that were difficult to recycle and energy-intensive production processes. However, the situation is very different today.
Over 7,000 people are employed by Nissan at its car manufacturing plant in Sunderland, which is northeast of England.
The factory has become efficient in several ways:
- Electric Vehicle Production: Nissan’s introduction of the LEAF, one of the world’s best-selling electric vehicles, marked a major shift towards sustainable automobile production. This zero-emission vehicle reduces reliance on fossil fuels and lowers greenhouse gas emissions.
- Energy Efficiency: The plant has implemented various energy-saving measures. These include using renewable energy sources, such as solar panels and wind turbines, to power operations, significantly reducing the factory’s carbon footprint. The site has ten wind turbines generating 6.6MW and 19,000 photo-voltaic panels (solar panels) generating 4.75MW of energy. This equates to 7% of the plant’s electrical requirements, enough to build 31,374 vehicles. CO2 levels have been reduced by 22.4% since 2005.
- Waste Reduction and Recycling: Nissan’s commitment to waste management involves minimising production waste and maximizing recycling. The plant operates under a zero-waste-to-landfill policy, ensuring all manufacturing waste is reused or recycled.
- Sustainable Supply Chain: Nissan collaborates with suppliers to ensure sustainable practices throughout its supply chain. This includes sourcing eco-friendly materials and ensuring suppliers adhere to environmental standards.
- Water Conservation: The factory employs advanced water conservation techniques, such as rainwater harvesting and water recycling systems, to reduce water usage in vehicle production.
- Education: The Skills Academy for Sustainable Manufacturing and Innovation (SASMI) supports the industry’s future through specialist training. Based at Nissan’s Sunderland plant, SASMI provides a training infrastructure for sustainable manufacturing and the low-carbon vehicle industry and a learning facility for employers, apprentices and students, providing new skills for new jobs.
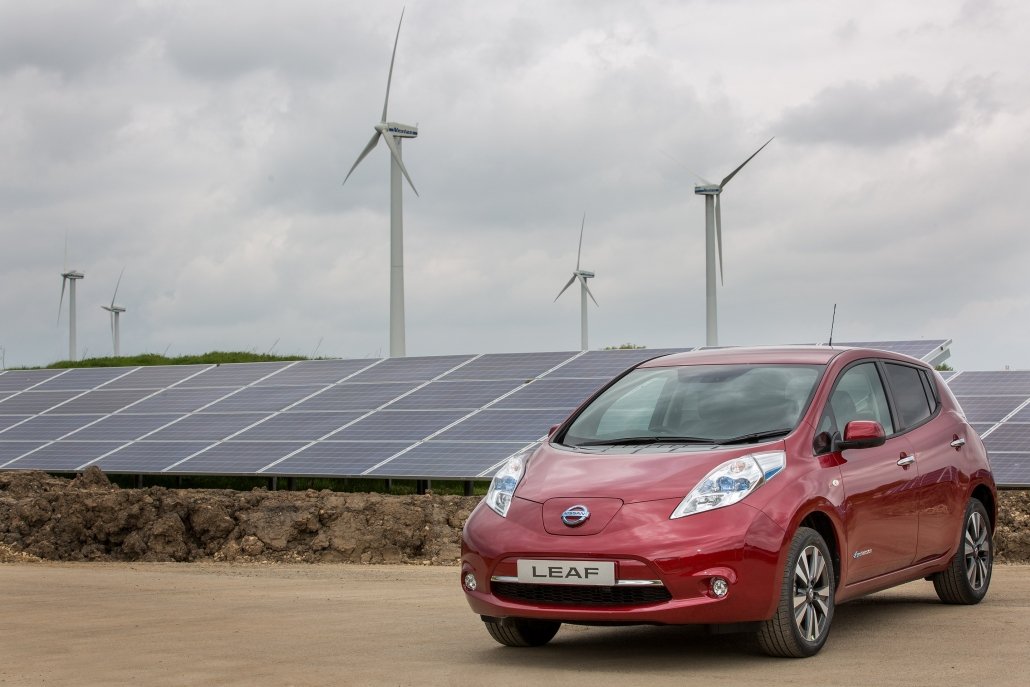
Wind turbines, solar panels and the Nissan Leaf at the Nissan factory, Sunderland
Summary
Flashcards
Coming soon
Check Your Knowledge
Coming soon
Test Yourself
Coming soon